Transform your landscape into the backyard paradise of your dreams with a functional and aesthetically pleasing Retaining Wall. But beware; these structures aren’t cheap.
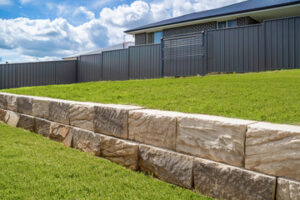
They also require routine inspections and maintenance to ensure they last. This is why it is important to choose a contractor with experience. The right contractor will help you avoid costly repairs down the road.
A retaining wall is an important addition to any property, as it can prevent soil erosion and boost the home’s value. It can also improve the layout of the terrain and prevent drainage problems. In addition, it can be designed to enhance the aesthetic of the yard and create a focal point. The cost of a retaining wall depends on the method of construction and the materials used. For example, a wall that is designed for seating requires special engineering and will increase the cost. However, walls that are below 4 feet don’t require this special design and can be constructed with a CMU block core and attractive veneer, which lowers the overall cost of the project.
Retaining walls come in a variety of materials, ranging from poured concrete to cinder blocks. The type of material chosen will affect the cost of the wall, but it is important to consult with a professional before making a decision. They will be able to give you advice on the best materials for your landscaping needs.
The cost of a retaining wall also depends on the location and size of the project. A retaining wall built on a steep slope will usually be more expensive than one built on flat land, as it will require ground regrading and other prep work before construction begins. In addition, the retaining wall will need to be engineered to withstand lateral earth pressure.
Generally speaking, the average cost of a retaining wall will be between $25 and $50 per square foot. However, it can vary significantly from project to project. There are many factors that can affect the cost of a retaining wall, such as the size of the wall, the material, and the labor.
Another factor that affects the cost of a retaining wall is the complexity of the project. Some retaining walls are simple, while others may be more complex and require excavation or tiebacks. The final cost of a retaining wall will depend on the level of complexity and how much the contractor charges for their services.
Design
A retaining wall is a structural support that holds back soil. It can be built for a variety of reasons, from landscaping to erosion control. The design of a retaining wall is important to ensure its stability. The wall’s base must be wide enough to distribute the earth’s pressure evenly. The height of the wall should also be sufficient to prevent it from sliding or overturning.
A sloping retaining wall is more stable than a vertical one. The slope of the wall should be at least a third of the vertical height of the wall. The wall must also be designed to resist the lateral earth pressures that push against it. These pressures increase with the height of the wall and are aggravated by groundwater. The design of a retaining wall must take into account the amount of lateral earth pressure and the surcharge load. It must also consider the bending and shear forces that occur in the wall stem and footings.
Retaining walls are often constructed on steep slopes to prevent soil erosion and landslides. They can also be used to stabilize slopes on roads, railways, and other infrastructure projects. They can be built using a variety of materials, including concrete blocks, poured concrete, treated timbers, and rock or boulders.
There are many different types of retaining walls, including cantilever and gravity walls. Some are made of natural rock and are more aesthetically pleasing than others. Some are even made of wood and designed to look like natural landscape features.
The process of building a retaining wall starts with excavating the site and backfilling the area behind the structure. The contractor then installs drainage, depending on the type of retaining wall being built. If a retaining wall will be anchored, the contractor will pour a slab foundation before beginning construction. Otherwise, the contractor will begin by building a dry stack wall or a masonry wall, then add reinforcement as they reach a certain height.
When constructing a retaining wall, the contractor must choose a material that is both durable and cost-effective. Landscaping with concrete blocks is a good option because they are easy to work with and give the wall a clean, finished look. The blocks must be laid in courses with staggered joints. This will help reduce the chance of cracking and will add to the longevity of the retaining wall. In addition to ensuring the strength of the wall, it is crucial to make sure that all penetrations are properly sealed to avoid water damage.
Materials
The materials used to construct a retaining wall can vary depending on the project. For example, poured walls can offer more design options than block walls. However, they are more expensive and require specialized skills to build properly. They are also not a good choice for taller walls, as they can crack or wave if the wall is not properly supported. In contrast, a concrete block wall can be built for less than a poured wall and may provide more design flexibility.
The material of a retaining wall determines its strength and durability. Generally, the thicker the wall, the greater the stress it must withstand. This is due to the fact that a retainer wall is designed to restrain soil at an angle steeper than its natural slope or incline, which creates lateral earth pressure on the backfill. Unless this lateral pressure is countered, the wall will eventually fail.
Retaining walls can be made from a variety of materials, including timber, interlocking blocks, and poured concrete. Timber walls are the least expensive option, but they are not waterproof and can rot in contact with moisture. They are typically limited to four-foot heights. For an extra $20 per square foot, you can upgrade to a wall constructed from interlocking blocks or poured concrete. These walls are more durable and can be a beautiful addition to your landscape design.
Brick is another time-honored material for constructing retaining walls. It is strong and can be used in a wide range of design styles, but it is expensive and labor-intensive to construct. A retaining wall that is constructed with brick can be expected to last for decades, but it will need regular maintenance and care to preserve its structural integrity.
A retaining wall must be constructed with proper drainage in order to avoid a buildup of water behind the wall. This water can cause the retaining wall to shift and even collapse. In order to prevent this, the wall should be designed with a well-draining backfill. This can be achieved by grading the backfill surface to direct water away from the wall or by directing water for disposal through drainage channels close to the retaining wall.
Maintenance
Retaining walls are designed to hold back soil, which would shift along a natural slope or incline if the wall were not there. However, over time, they can deteriorate due to poor construction, a lack of maintenance, and seasonal changes. This can affect their stability and pose a safety risk. If a retaining wall is showing signs of deterioration, it’s important to act fast to prevent it from collapsing.
A retaining wall should have a drainage pipe to move water away from the base. This is especially important during the winter, when snow and ice can clog the drain. It is also important to keep the soil in the area around the retaining wall healthy and free of weeds. Regular inspections and weed removal can prevent the ground from shifting, which could cause the retaining wall to deteriorate or collapse.
If your retaining wall is damaged, you’ll want to contact a contractor right away. A quick fix can save you a lot of money in the long run. If the retaining wall is still structurally sound, it may be able to be repaired. However, in some cases, the entire wall will need to be replaced.
One of the most common causes of retaining wall failure is improper drainage. Wet soil is incredibly heavy and can quickly damage a wall that wasn’t built to support it. Improper drainage can also cause the soil to build up behind a retaining wall, which can also cause damage.
If the retaining wall has been impacted by seasonal weather or poor construction, it’s important to take steps to fix it as soon as possible. Retaining walls that don’t receive proper care will deteriorate, causing them to crack, rot, or even collapse.
Another common problem is that a retaining wall doesn’t have enough tiebacks. Tiebacks are anchor rods that help stabilize a retaining wall by tying it into the soil behind it. These are generally installed using helical anchors, which are driven through holes in the retaining wall and then connected to earth anchors in augured holes in the soil.
Retaining walls are essential for holding up areas of your yard or garden. They can be constructed from wood, masonry, or concrete blocks. They can be used to create a curved or straight elevation in your yard, and they can add an aesthetic element to the landscape design. They can be expensive to build, but addressing small problems as they arise will prevent them from becoming more costly down the line.